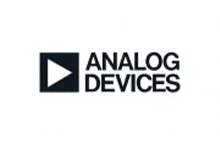
- Analog Devices
- NEXT Mobility
- ICT and Industrial
Motion Controllers and Motor Drivers for Stepping Motors
Analog Devices' industry-leading motion control products feature a hardwired architecture delivering improved energy efficiency, stall prevention, and reduced motor noise and vibration. This makes them ideal for integration into products requiring advanced control, such as robotics, medical equipment, and 3D printers. In addition to mechatronic solutions including ICs and motors, we provide the TMCL IDE integrated development environment to accelerate application development.

Features
- Hardwired architecture integrates control algorithms for power saving, quiet operation, and reduced downtime.
- Parameters like position, velocity, and acceleration can be changed on the fly.
- The TMCL IDE integrated development environment enables efficient plug-and-play development.
Functionality
StallGuard™
A sensorless stall prevention algorithm minimizes downtime. Surplus energy supplied to the motor, which serves as a measure of mechanical load, is estimated from the back EMF generated during rotation. If this surplus energy is depleted, the motor can stall. This function prevents the motor from losing synchronization by stopping rotation before the surplus energy runs out.
SteathChop
Sensorless load detection and automatic current control ensure the motor is always controlled with optimal current, reducing power consumption. StallGuard reduces surplus energy by appropriately controlling the supply current based on the estimated surplus energy value. The graph below, obtained with the TMCL IDE integrated development environment, shows that the motor drive current decreases when the preset SG value (surplus energy) is large. Conversely, when the mechanical load increases, the SG value decreases, but the motor drive current is automatically increased to prevent stalling.

StealthChop™
This technology achieves ultra-quiet, low-speed operation by minimizing audible noise caused by magnetostriction. In current mode PWM control, like SpreadCycle, the control is affected by the current sensing value of each PWM cycle, leading to the drawback of increased motor current ripple in response to slight noise. StealthChop employs voltage mode PWM control to reduce current ripple, suppress magnetostriction vibration in the stator materials, and reduce audible noise.
-
SteathChop
-
SpreadCycle
Motor drive current
-
SteathChop
-
SpreadCycle
Motor drive current (green) and drive voltage (light blue, yellow)
Product Categories
Driver
These devices integrate all necessary functions, including pre-driver, sensing, protection, and power output stage circuits, into a single package. Features such as StallGuard, StealthChop, and CoolStep are implemented via hardwired architecture, with a product lineup supporting various voltage and current ratings. The motor is driven based on the input Step/Dir signals.
Motion Controller
A motion controller generates Step/Dir signals based on input parameters such as position, velocity, and acceleration, which can be changed on the fly during operation. This eliminates the need for the main microcontroller unit (MCU) to generate Step and Direction signals, significantly reducing the MCU's computational load, development effort, and demanding real-time processing requirements.
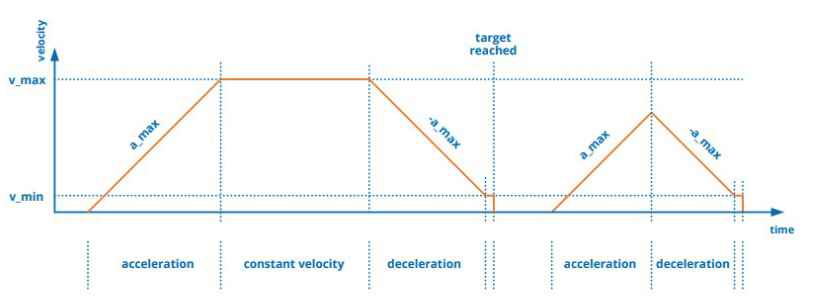
The trapezoidal ramp profile accelerates at a constant rate until reaching maximum speed, then decelerates at a constant rate to stop at the designated position. This helps reduce real-time processing from demanding MCUs.
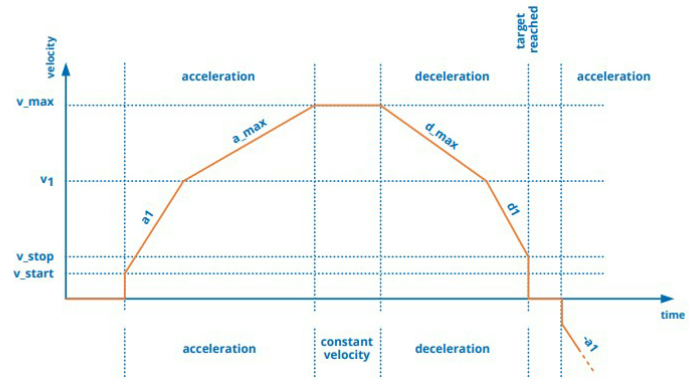
Acceleration and deceleration rates can each be configured in two distinct stages. This feature makes it possible to reduce vibration and audible noise associated with sudden speed changes.
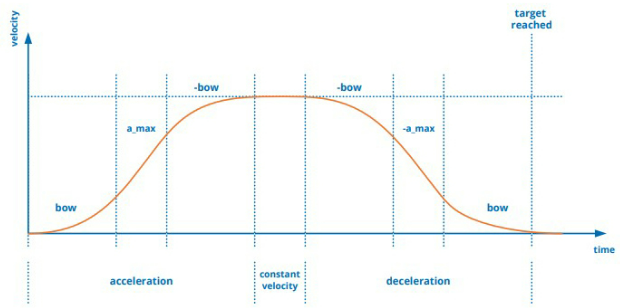
Alternatively, the S-shape profile achieves smoother speed transitions by gradually changing acceleration and deceleration. This gradual change helps reduce vibration and audible noise often caused by abrupt speed shifts. The S-shape profile's ability to minimize resonance-induced vibration makes it particularly suitable for applications sensitive to disturbances, such as those involving liquids.
Difference between S-shape and trapezoidal patterns
CDriver™
CDriver integrates a driver and motion controller into a single IC.
Module
The module offers a full-featured board-level solution, suitable for applications including lab automation, manufacturing, industrial automation, medical, and robotics. Utilizing TMCL-IDE, it also supports standalone operation, eliminating the need for a HOST controller.
PANdrive
This product combines a motor and a module.
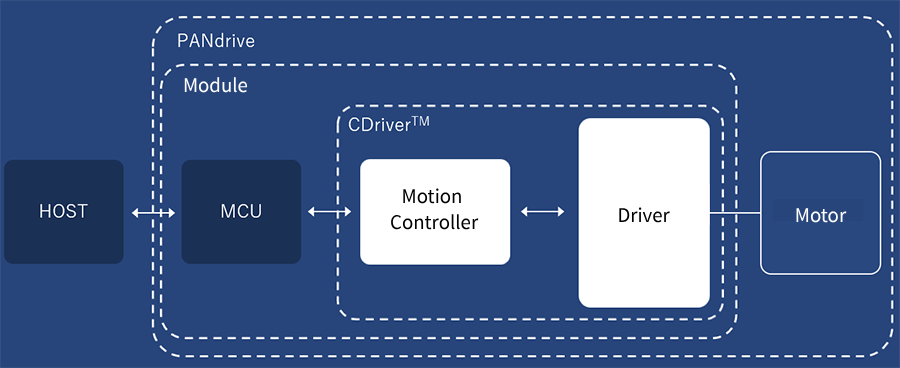
Integrated Development Environment (TMCL-IDE)
The Integrated Development Environment, or TMCL IDE, stands for Trinamic Motion Control Language Integrated Development Environment. It is specifically designed for developing applications that use ADI Trinamic™ modules and chips. This graphical user interface provides tools allowing users to easily configure parameters, visualize data in real time, and develop standalone applications.
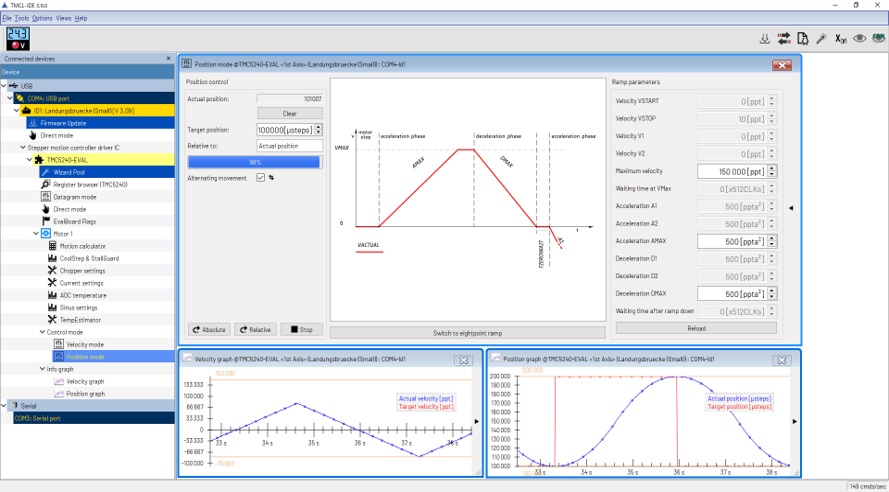
Inquiry
Related Product Information
Low-Noise Switching Regulator Suitable for Power Supply in RF Products
Silent Switcher 3 is the latest switching regulator technology that achieves low low-frequency noise and fast load response.
- Analog Devices
- ICT and Industrial
Using AI Machine Learning to Diagnose Motors - The Smart Motor System
With the ADI OtoSense Smart Motor Sensor, let AI handle everything from threshold setting to analysis, diagnostics, and root cause identification—preventing downtime and avoiding losses.
- Analog Devices
- NEXT Mobility
- ICT and Industrial
- Smart Factories and Robotics
New LTspice③ Parametric Analysis and Tolerance Analysis
LTspice is a free SPICE simulator provided by Analog Devices. This article introduces methods for parametric and tolerance analysis, as well as how to use dot commands.
- Analog Devices
- NEXT Mobility
New LTspice②: How to Use SPICE Models
LTspice is a free SPICE simulator provided by Analog Devices. This article introduces how to obtain demo circuits and various models.
- Analog Devices
- NEXT Mobility
New LTspice Complete Guide ①
LTspice is a free SPICE simulator provided by Analog Devices. This article explains the updates and performance improvements in the latest version, LTspice24.
- Analog Devices
- NEXT Mobility
Introduction to Wireless Gesture Sensors (Use Cases for Analog Devices Products)
The wireless gesture sensor developed by NEXTY Electronics enables remote control of home appliances and display devices at low cost.
- Analog Devices
- NEXT Mobility
- ICT and Industrial
- Smart Factories and Robotics